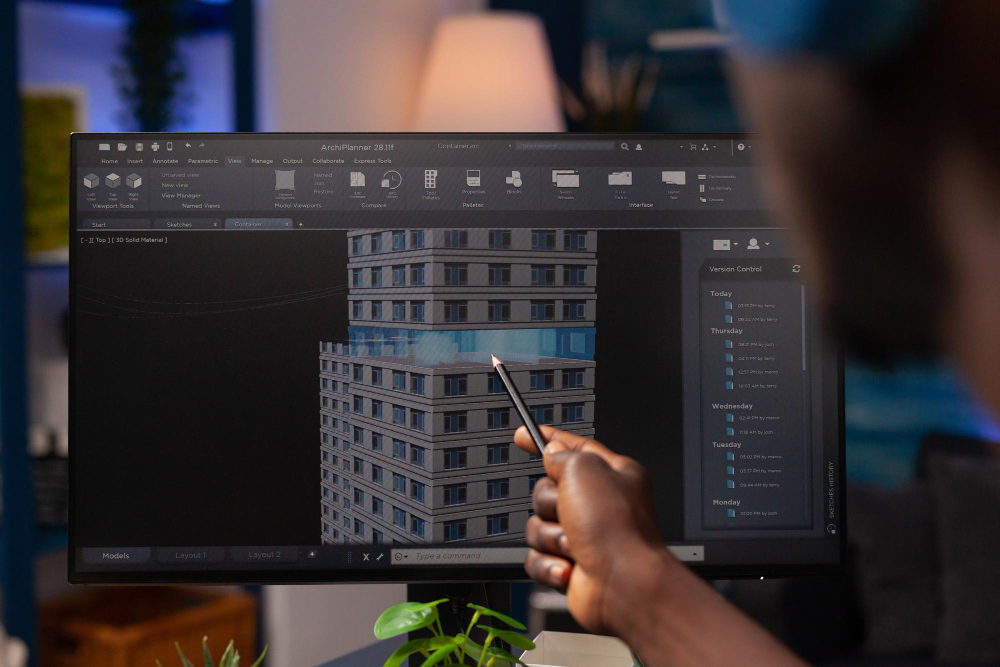
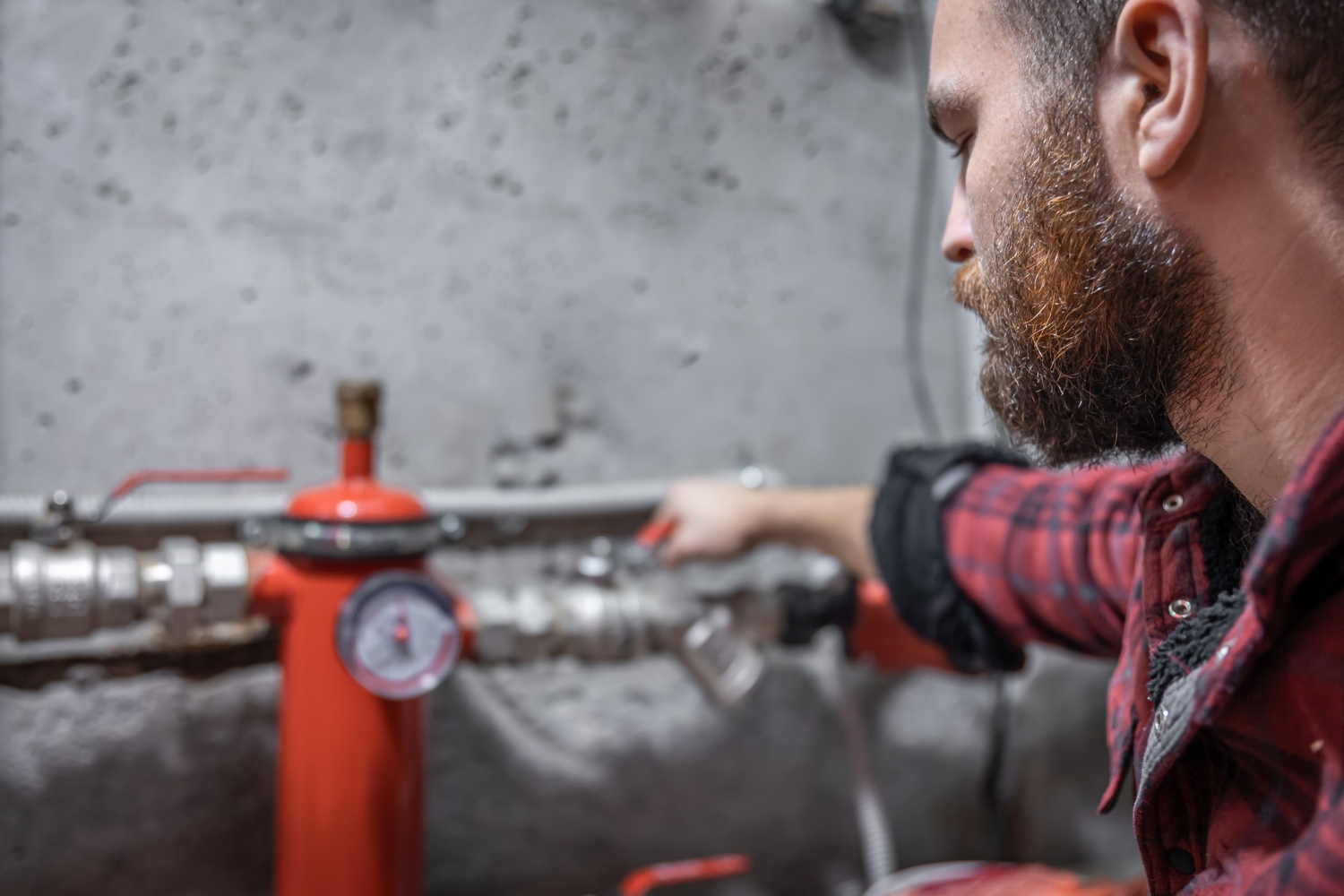
In the bustling world of commercial operations, gas systems play a pivotal role in ensuring smooth and efficient functionality. From powering heating systems to fueling industrial processes, these systems are the backbone of many businesses. However, like any mechanical system, they are prone to wear and tear over time. This brings us to a critical decision point: Should you adopt a reactive or preventative maintenance approach for your commercial gas systems?
In this blog post, we’ll delve deep into understanding both maintenance strategies, weigh their pros and cons, and help you decide what’s best for your business.
What is Reactive Maintenance?
Reactive maintenance, often termed “breakdown maintenance,” is a strategy where no actions or efforts are taken to maintain equipment until a failure occurs. In simple terms, “If it’s not broken, don’t fix it.”
Pros of Reactive Maintenance
- Lower Immediate Costs: Since maintenance is only performed when necessary, there are no ongoing maintenance expenses.
- Simplicity: Easier to manage as it doesn’t require scheduling or planning.
- Short-Term Focused: Ideal for equipment that’s inexpensive or easy to replace.
Cons of Reactive Maintenance
- Unexpected Downtime: Equipment failure can lead to unplanned operational halts, affecting productivity.
- Higher Long-Term Costs: Emergency repairs and replacements can be more expensive than regular maintenance.
- Safety Risks: Sudden failures can pose significant safety hazards, especially with gas systems.
- Reduced Equipment Lifespan: Lack of regular maintenance can lead to accelerated wear and tear.
Reactive Maintenance in Commercial Gas Systems
Applying reactive maintenance to commercial gas systems can be particularly risky. Gas leaks, system failures, or malfunctions can not only disrupt operations but also pose severe safety threats, including fire hazards and exposure to toxic gases.
What is Preventative Maintenance?
Preventative maintenance involves regular, planned maintenance activities designed to prevent equipment failures before they occur. This strategy is proactive, focusing on minimizing downtime and extending equipment life.
Pros of Preventative Maintenance
- Reduced Downtime: Regular checks and maintenance reduce the likelihood of unexpected failures.
- Cost Savings Over Time: Preventing major repairs and extending equipment lifespan can lead to significant savings.
- Enhanced Safety: Regular inspections ensure that any potential safety issues are identified and rectified promptly.
- Improved Efficiency: Well-maintained equipment operates more efficiently, saving energy and operational costs.
Cons of Preventative Maintenance
- Higher Immediate Costs: Regular maintenance requires an upfront investment.
- Resource Intensive: Requires time and skilled personnel to perform maintenance tasks.
- Potential for Over-Maintenance: Without proper planning, there’s a risk of performing unnecessary maintenance.
Preventative Maintenance in Commercial Gas Systems
For commercial gas systems, preventative maintenance is often the recommended approach. Regular inspections can detect issues like gas leaks, pressure irregularities, or component wear before they escalate into major problems.
Reactive vs. Preventative Maintenance: A Comparative Analysis
Cost Implications
- Reactive Maintenance: May seem cost-effective initially but can lead to higher expenses due to emergency repairs, operational downtime, and potential regulatory fines.
- Preventative Maintenance: Involves regular costs but can save money in the long run by avoiding major repairs and extending equipment life.
Safety Considerations
- Reactive Maintenance: Increases the risk of safety incidents due to unexpected equipment failures.
- Preventative Maintenance: Enhances safety by ensuring equipment is in good working condition and potential hazards are addressed promptly.
System Efficiency and Lifespan
- Reactive Maintenance: Can lead to decreased efficiency as equipment deteriorates without maintenance.
- Preventative Maintenance: Keeps systems running optimally, improving efficiency and extending the lifespan of equipment.
Regulatory and Compliance Considerations
Many regions have strict regulations governing the maintenance of commercial gas systems. Non-compliance can result in hefty fines, legal liabilities, and reputational damage.
- Reactive Maintenance Risks: Increases the likelihood of non-compliance due to unforeseen failures and neglected maintenance requirements.
- Preventative Maintenance Benefits: Helps ensure compliance with regulations through documented maintenance activities and regular inspections.
Making the Right Choice for Your Business
When deciding between reactive and preventative maintenance for your commercial gas systems, consider the following:
- Nature of Operations: If your business relies heavily on continuous operation of gas systems, unexpected downtime can be costly.
- Safety Priorities: In industries where safety is paramount, preventative maintenance is crucial.
- Budget Constraints: While preventative maintenance requires an upfront investment, the long-term savings and risk mitigation often justify the costs.
- Regulatory Requirements: Ensure your maintenance strategy aligns with legal obligations in your jurisdiction.
Case Study: The Cost of Neglect
A mid-sized manufacturing company opted for reactive maintenance to save on costs. One of their gas boilers, uninspected for years, developed a minor leak. Unnoticed, this leak led to a gas build-up, resulting in an explosion that halted operations for weeks, caused injuries, and led to significant financial losses due to repairs and legal liabilities.
Had the company invested in preventative maintenance, the leak could have been detected and repaired promptly, avoiding the catastrophic outcome.